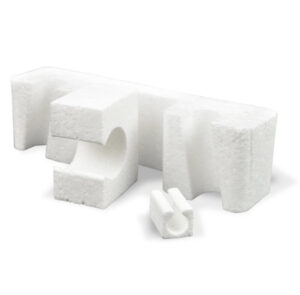
Protective packaging is an important consideration for any online retailer, shipper or business that moves freight. If you move hundreds or thousands of items regularly the impact of even the smallest decrease in protective packaging can result in huge savings over the course of the year.
Careful inspection into how you manage your protective packaging is not only important, it is necessary.
Right-Sizing Your Protective Packaging
Proper sizing of your foam and dunnage as well as the size of the box in use is of the utmost importance. Packaging that is too small will risk damaging the products and larger packaging than is necessary can hurt costs or even cause less effective protection as products move within the package.
It’s essential to use the appropriate size for your packaging needs based on the size, shape, and weight of each item. Choosing the right box and protective packaging that allows the items to be appropriately cushioned while also not allowing it to shift too much while in transit is always the goal.
Selecting the Right Materials
Be sure to select the proper foam materials to cushion your particular product. Certain types of foam are more effective at protecting items from different environmental hazards, and a careful analysis of your items and the protection they need will reduce damage claims. It is important to consider what types of protection your products need, including items that are sensitive to:
- Electrostatic discharges
- Abrasive surface
- Hot or cold temperatures
- Moisture or humidity
Review the various pros and cons for every foam type available to be sure to use the most effective solutions for your needs.
Work with the Right Foam Provider
You know your products better than anyone else. The right foam provider will work with you to choose protective packaging that is not only effective, but cost efficient. Working with a reliable partner will inevitably lower your costs as product loss from damage in transit and the use of efficient and cost effective solutions will lead to a higher margin for your products. The right foam provider will have access to a variety of foam types, custom fabrication for protective packaging, and large production runs of custom foam pieces that allow you to purchase in bulk what you need for the long run.
At Rogers Foam, we specialize in custom protective packaging solutions provided with competitive pricing. We can help you properly protect the products you ship while lowering your costs and damage claims ratios. Reach out to use today to see how we can help you.