Foam Applications
Engineered foam products have an wide range of practical applications. Foam’s noise-insulating capability makes it an ultra-efficient sound absorber. Thicker foam layers better absorb lower frequency sounds, while thinner layers better absorb higher frequencies. Flame resistant silicone foams are ideal for demanding transportation applications. Reticulated urethane has a natural toughness that allows our customers to make bacteria filters as fine as 150 pores per inch.
Rogers has experience with many of these applications and many more, including acoustic, comfort and support, filtration, gaskets and seals, specialty packaging, medical positioners, surface protection, and thermal management. Our in-house engineering department can work with you to design a solution that meets even the most challenging set of performance requirements.
Comfort and Support
Foam can cradle you during sleep or support you during injuries. The unique properties of foam, in conjunction with our unique expertise with fluid penetration, adhesives, fabrics and ASTM-compliant coating for flame resistance allows us to meet even the most challenging applications. Our expertise also allows us to build to print or help you design your product from scratch. Comfort materials can range from luxurious high-resilient foams to form fitting viscoelastic foams; or, convoluted toppers and crisp safety rails for medical beds to long-life flame resistant silicone foams for demanding transportation applications.
Filtration
There are many filtration applications that can be filled by foam.
For example:
- Automotive pre-filters
- Small engine filters
- Oil-coated small particle filters
- Washable reusable filters
- Multi-layer progressive filters
- Oil – water separation
- Platforms for ceramic filters
- Platforms for molten metal filtration
Materials used for custom filter fabrication often benefit from the “reticulation” process, which removes the cell membranes and impurities, and greatly enhances urethane’s natural toughness. It enables us to make foams as course as 3 PPI (pores per linear inch) and as fine as 110 PPI for applications that range from hydrocarbon filters to makeup applicators.
Gaskets and Seals
Rogers’ engineering team is available to work with your engineers to design an effective air gasket or fluid seal. Our high speed manufacturing process will provide your company with the right part at an affordable cost, to spec, every time.
Materials for these applications include:
- Low-compression-set cast urethanes to rugged EPDM
- ECH and silicone cellular rubbers to economical neoprene blends
- Closed cell urethane
- Many more
Our team can combine these foams with films, adhesives, and other substrates to provide the performance needed.
Specialty Packaging
Rogers has over 40 years of experience making custom packaging solutions. One area of specialty is case inserts for demanding military and non-military applications. Our water jet machinery can consistently cut high profile, straight vertical walls in foam and assemble multiple layers to produce a case insert with various cavity depths. We can provide the exterior case, or use your preferred supplier, to deliver a turn-key packaging solution. Software support includes SolidWorks and CNC programming.
Thermal Management
As electronics replace mechanical movement in more and more products, thermal management has become critical to success. Manufacturers are packing smaller components into less space, and there’s an increased need to protect products from harsh environments. To meet this need, Rogers Foam uses its expertise to combine reflective foils and films, insulating foams and glass fibers, and thermal decouplers. Rogers has the ability to form nearly any shape to fit your design.
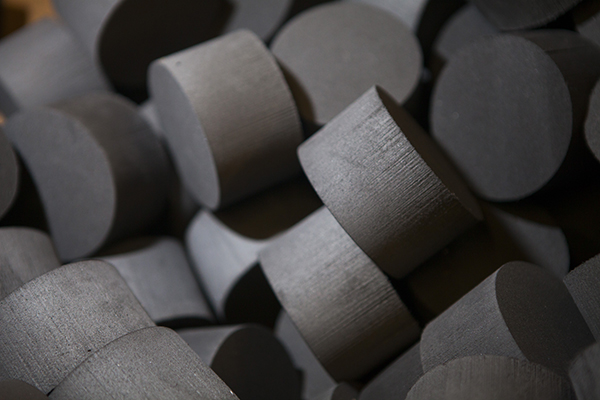
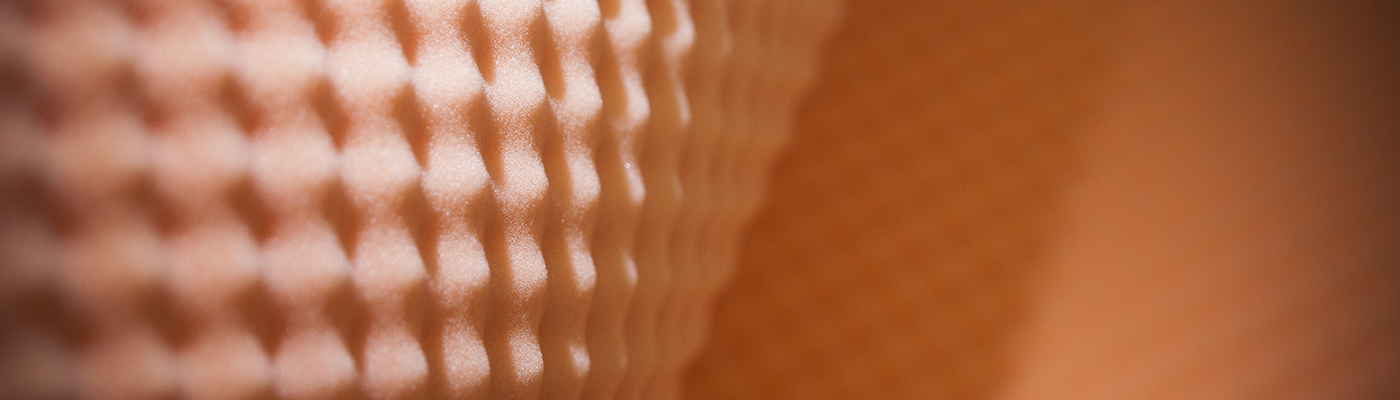
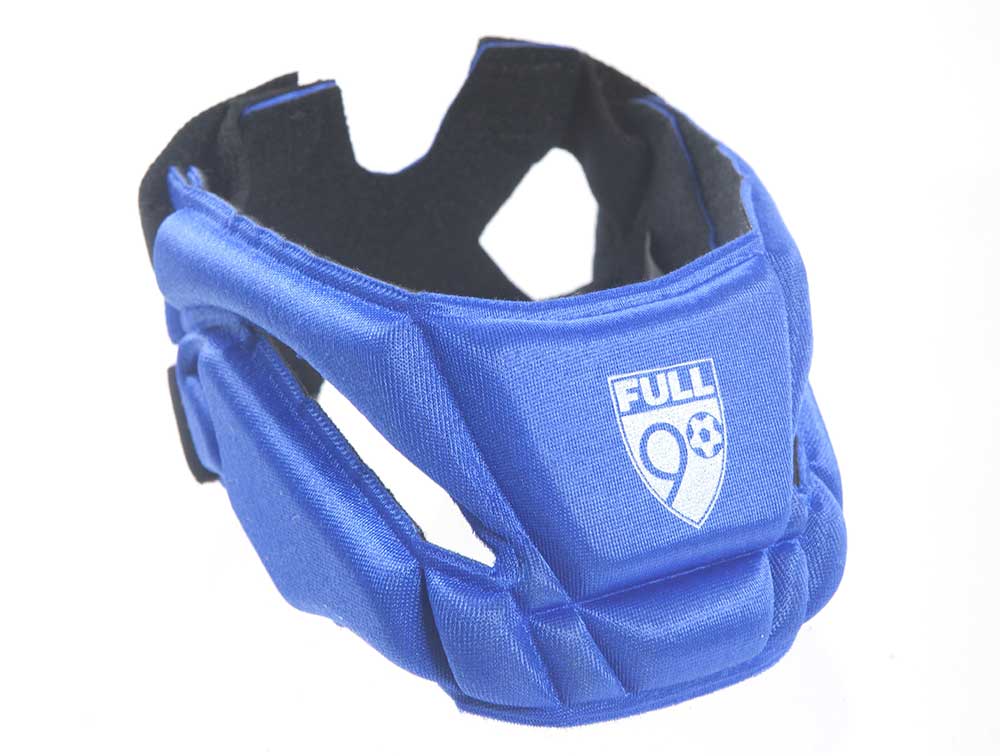
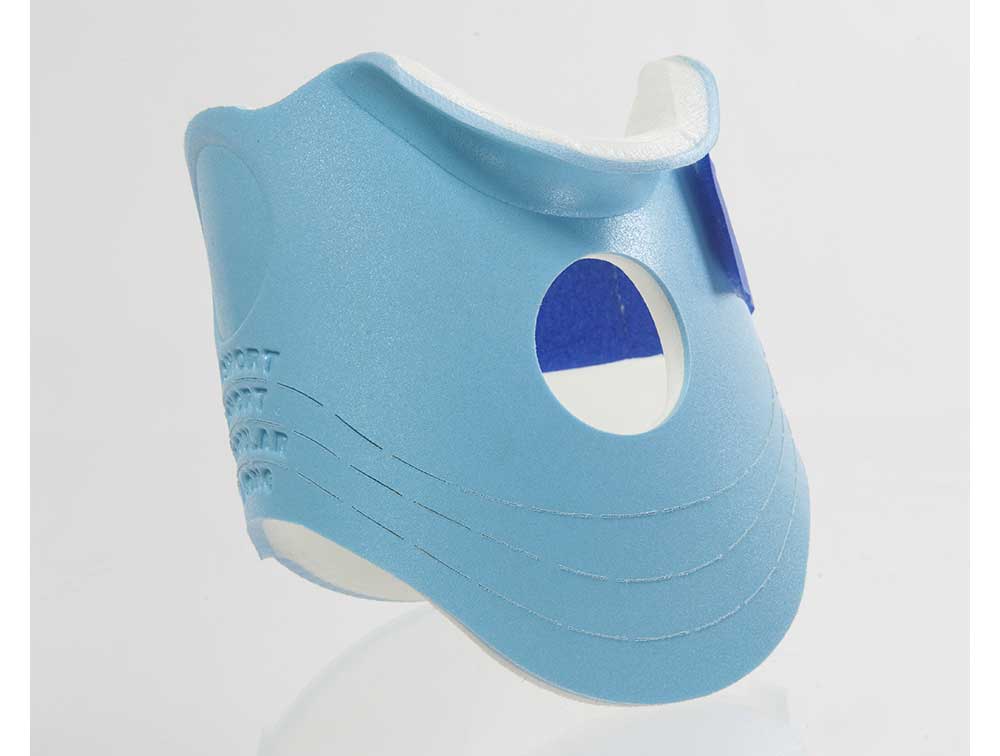
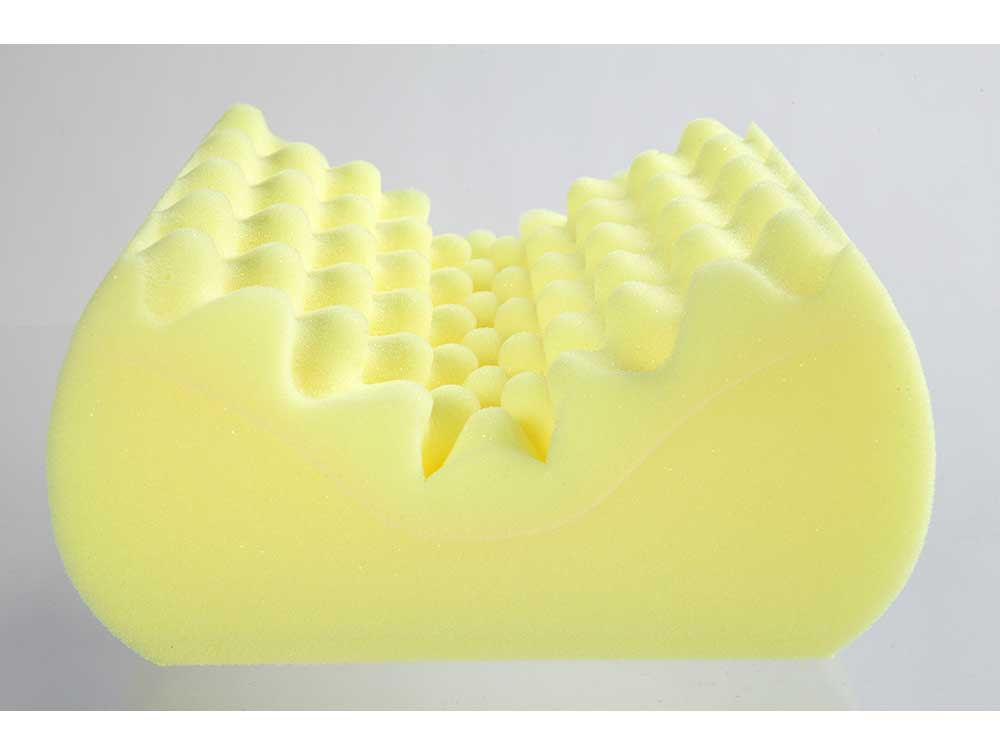
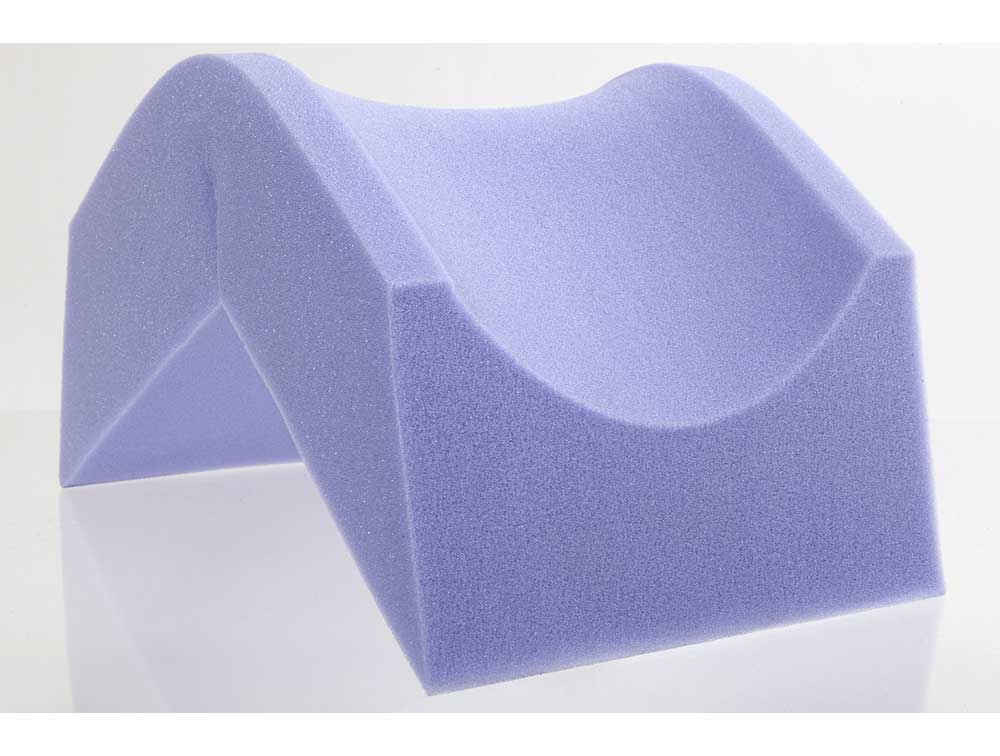
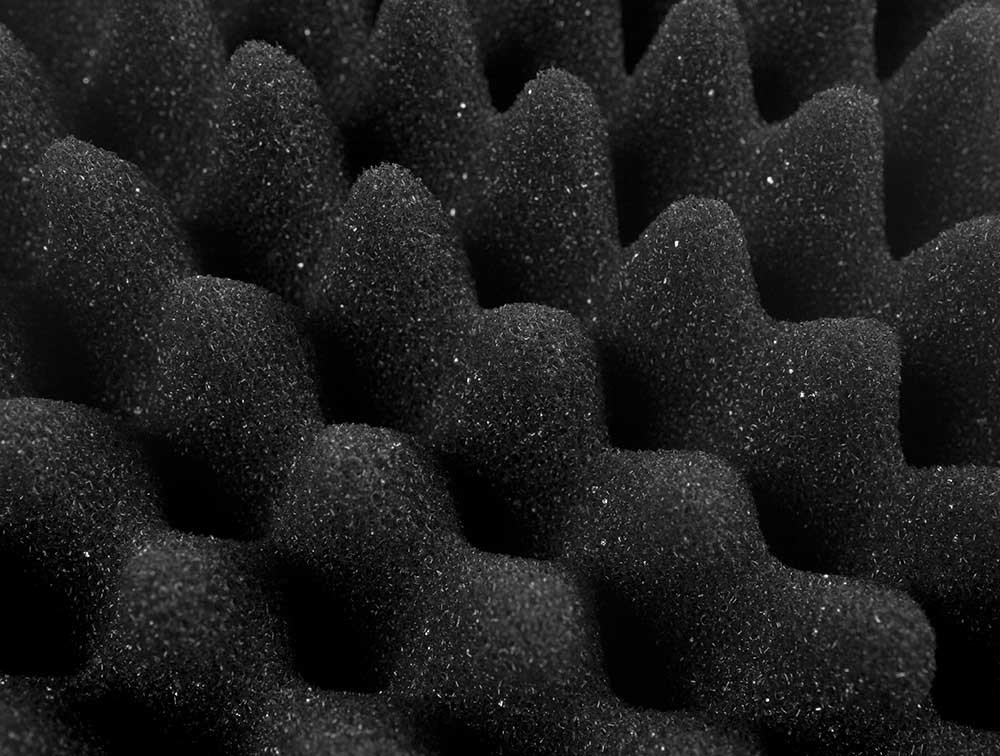
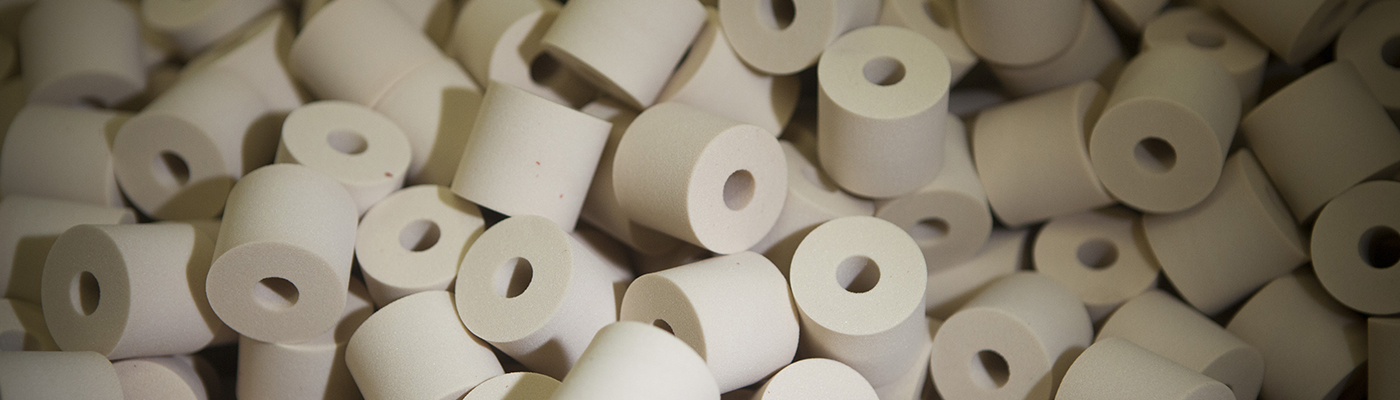
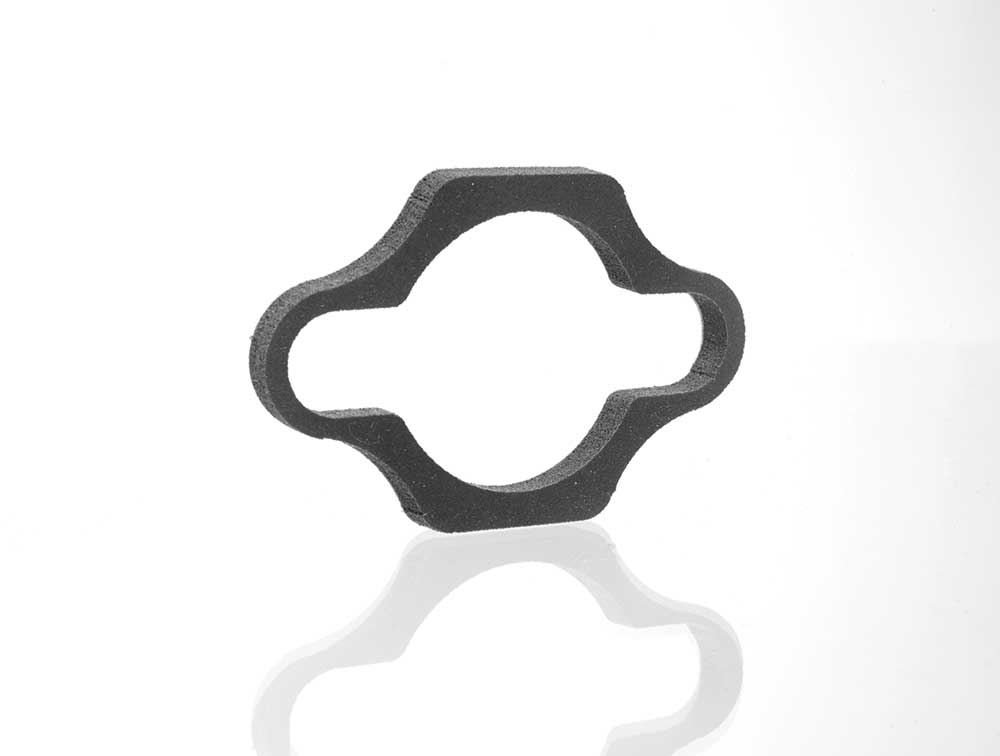
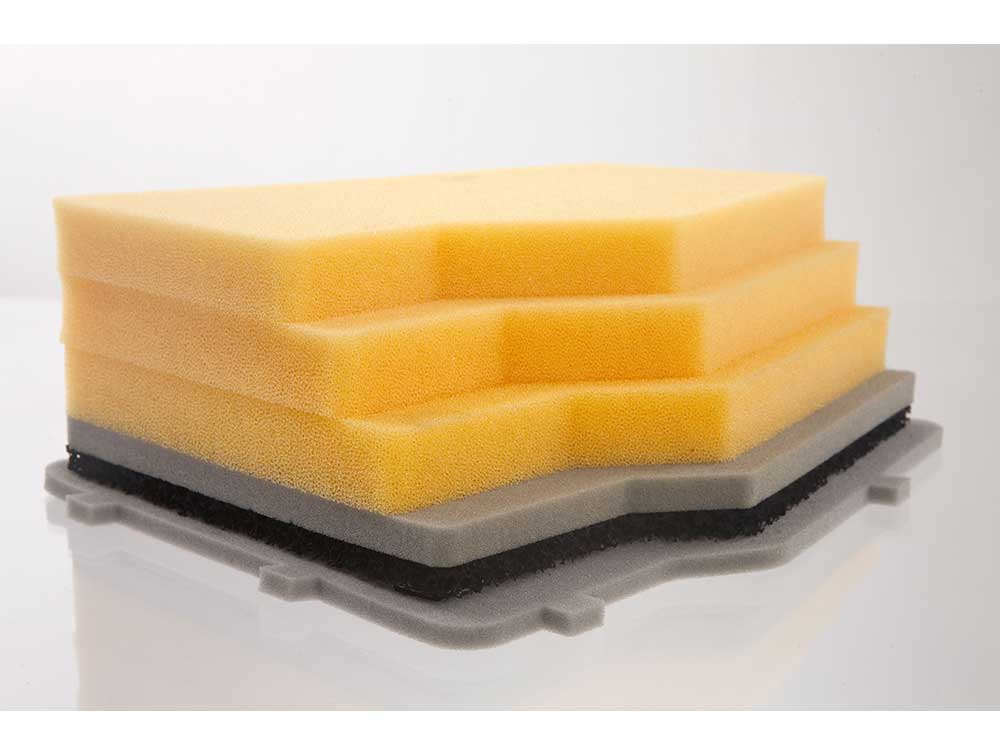
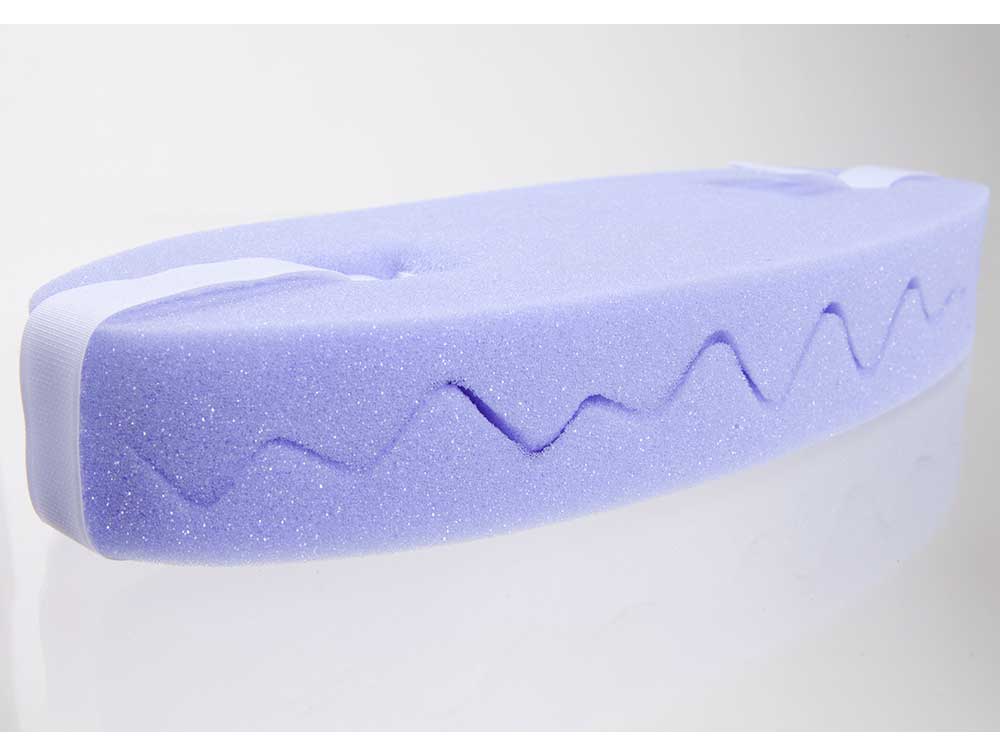
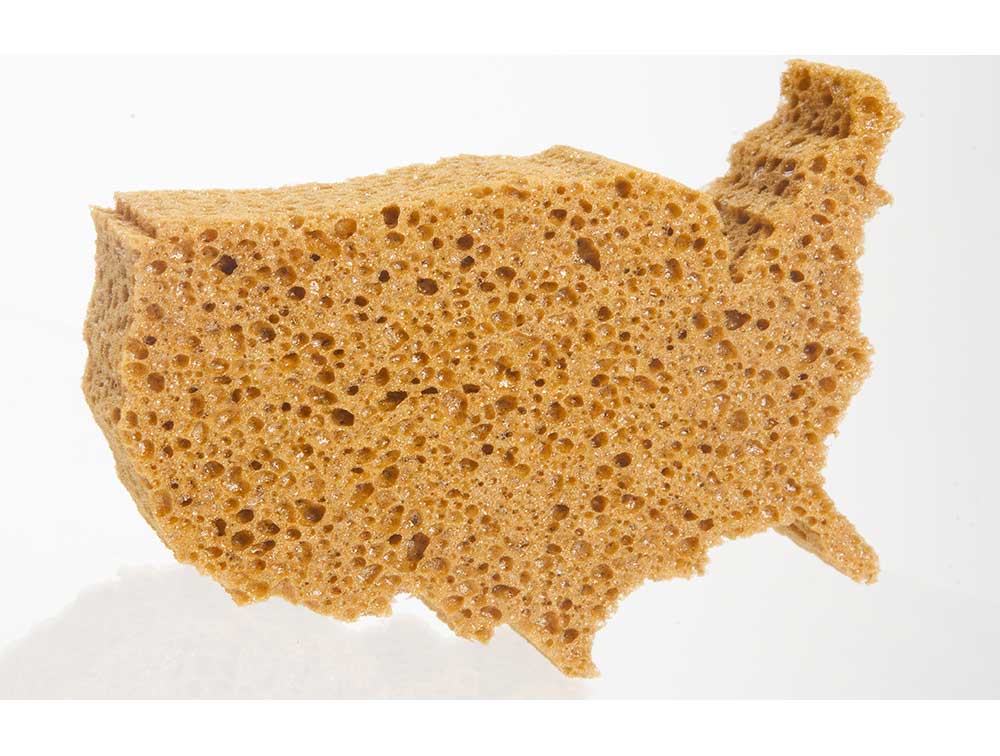
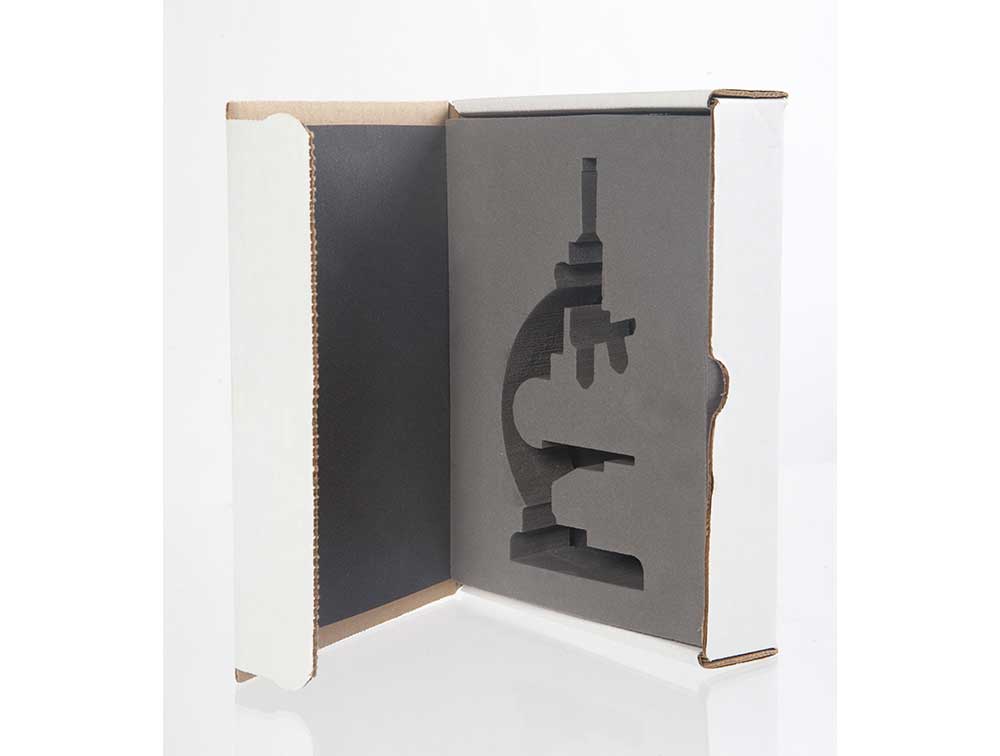
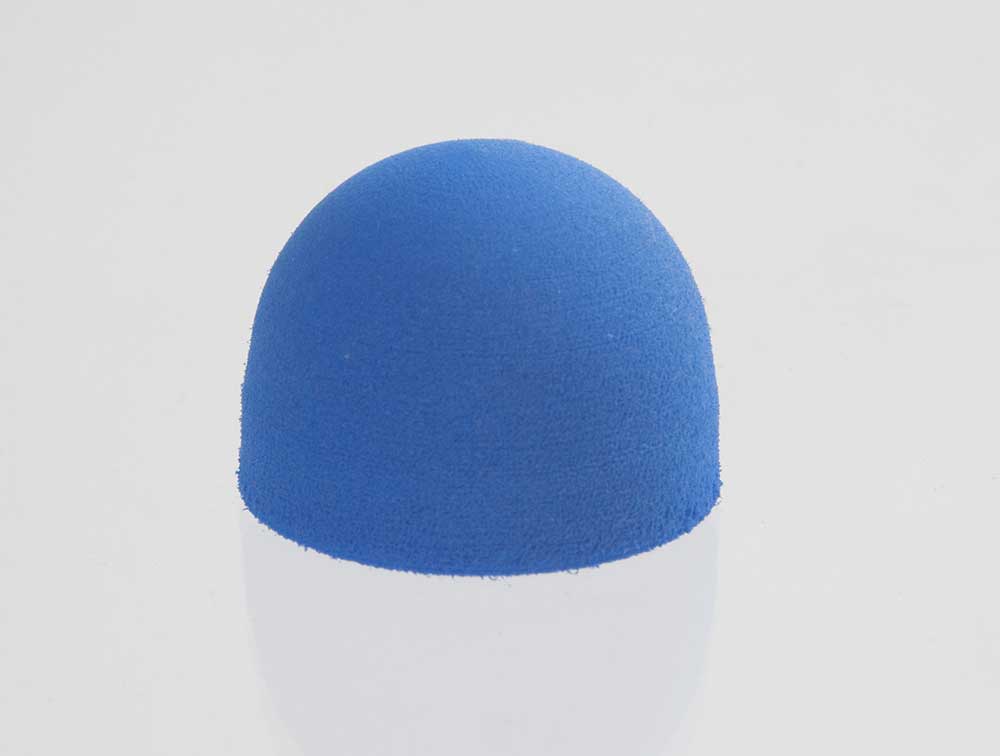
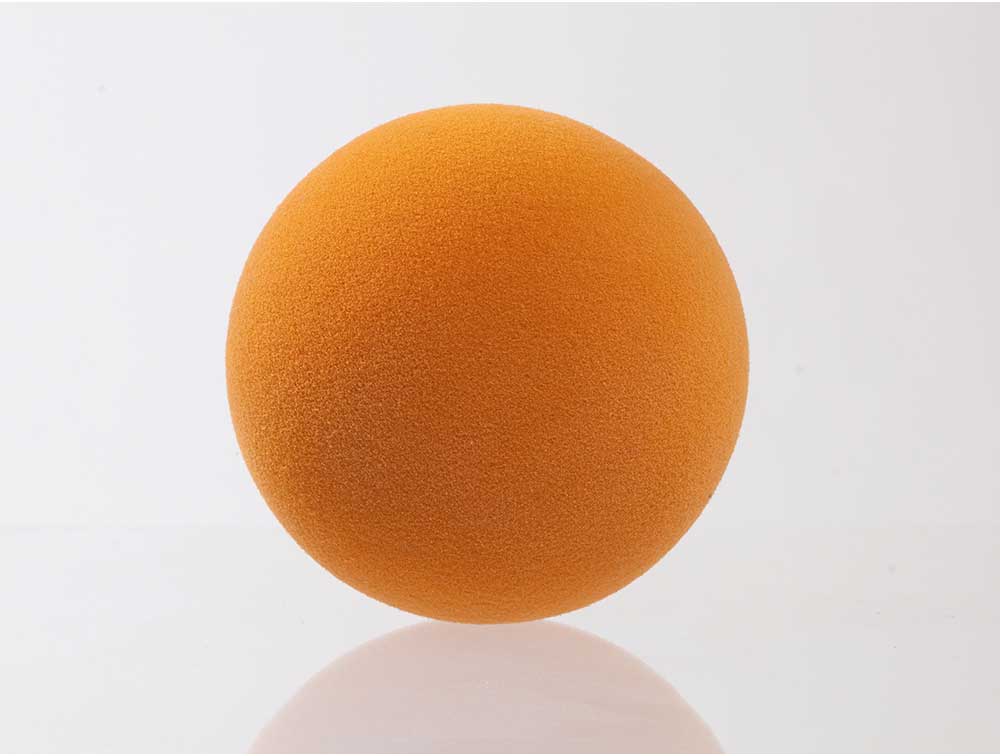
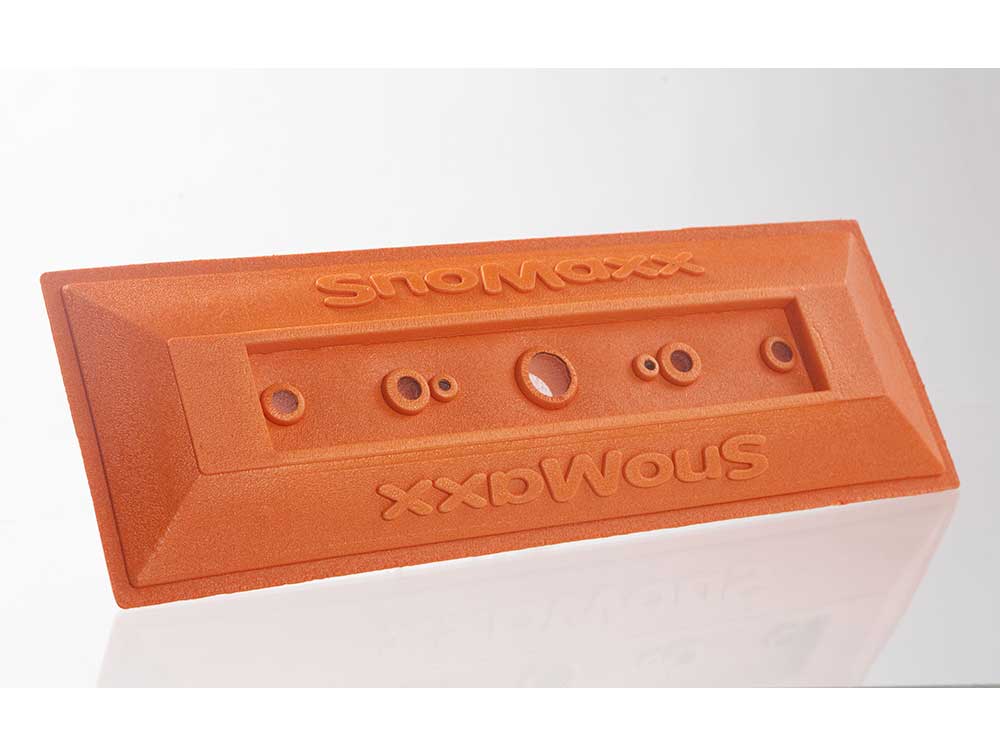
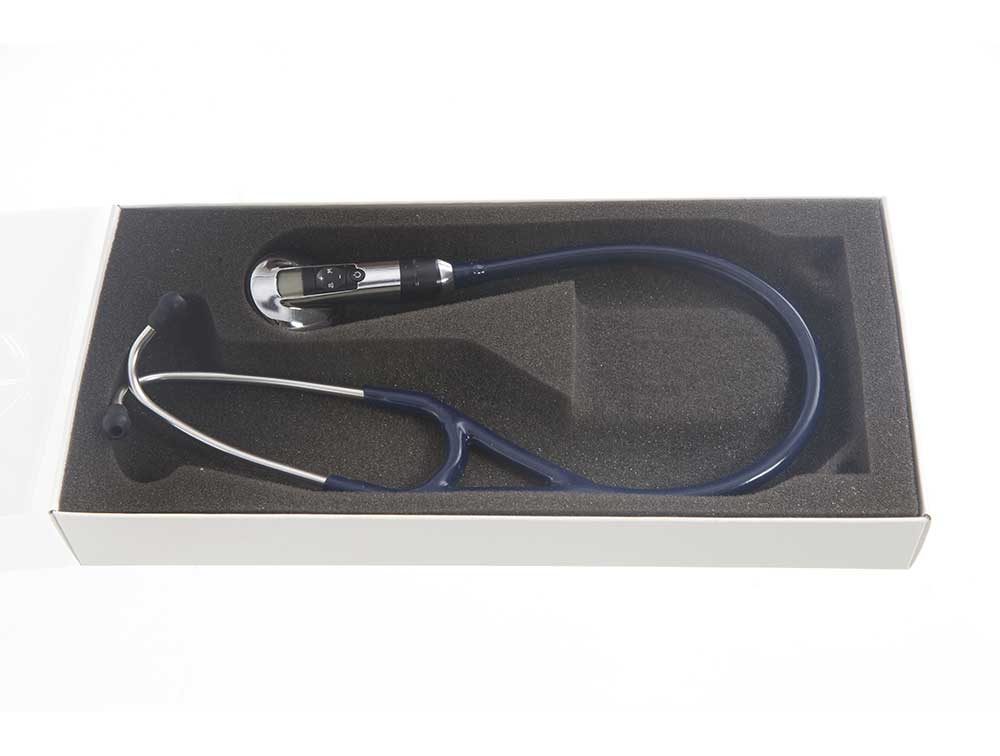
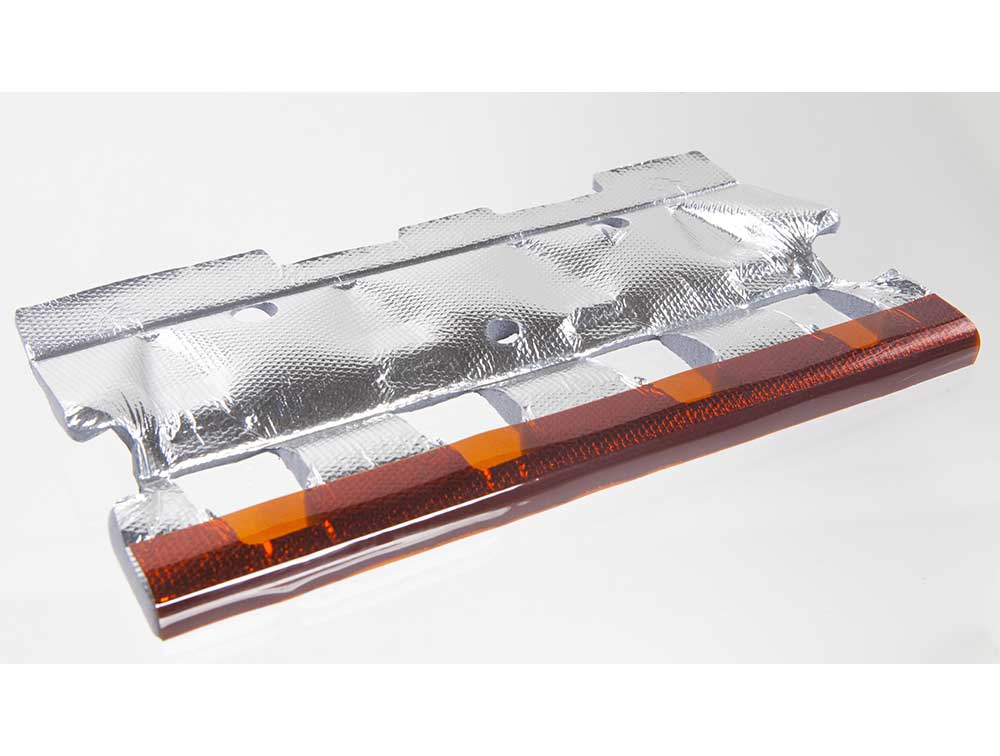

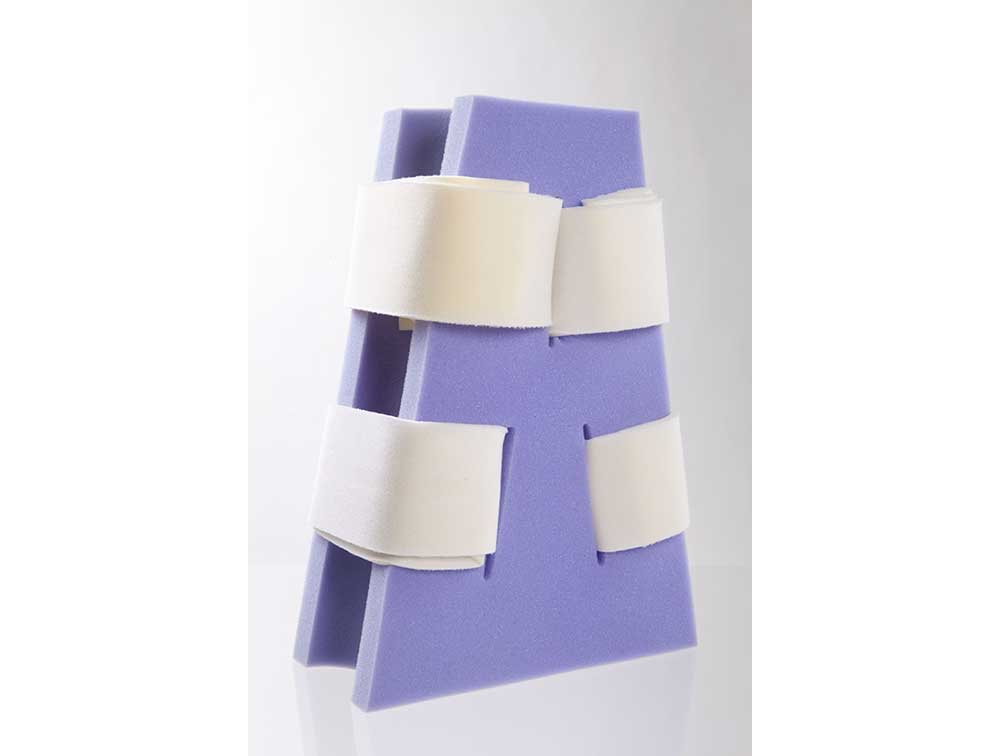
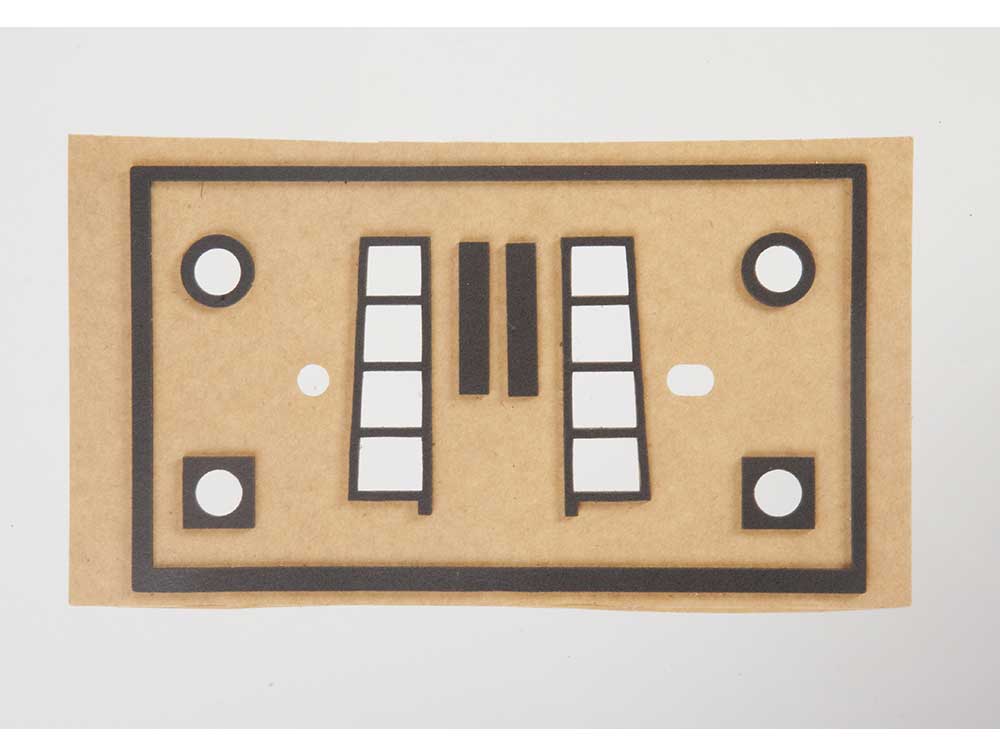
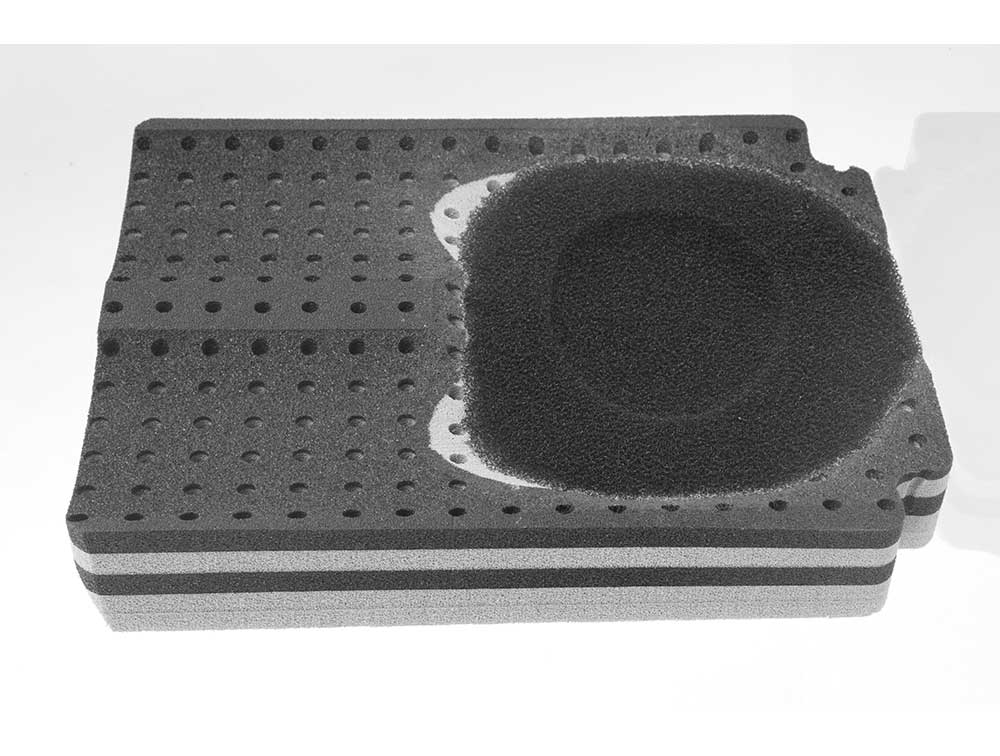
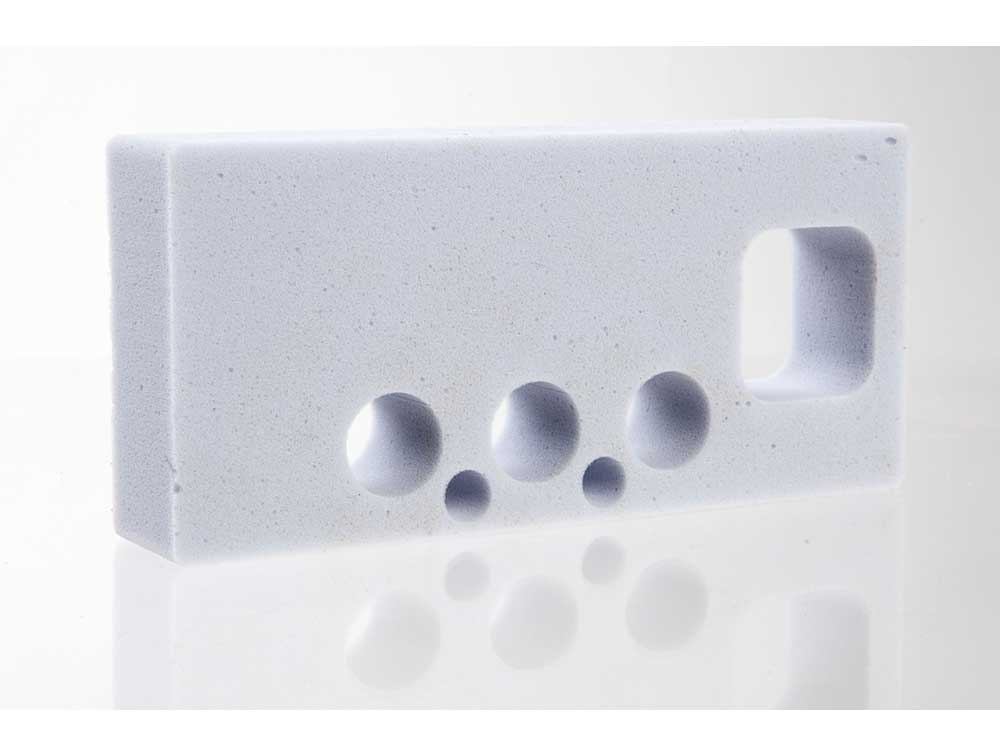