Reticulated Foam Applicator for Major Cosmetics Brand
Problem
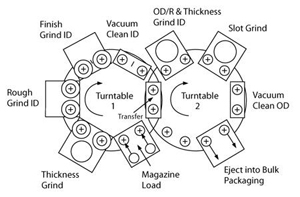
A major cosmetics company required a design for reticulated foam applicators with precise wicking and liquid retention properties for the launch of an important tanning lotion product. After the design was in place, the customer depended on Rogers Foam to manufacture 1.5 million applicators in less than four months.
Solution
To meet the exacting requirements, Rogers Foam sampled six reticulated foam grades and 30 different applicator shapes and sizes. The optimum applicator design incorporated reticulated foam with a 1.5 inch diameter, a ground shape on top and a ground shape within a blind hole on bottom. To ensure that the liquid is dispensed at the correct rate, the design called for a half millimeter tolerance on the metering thickness. A slot around the outside perimeter of the part held the foam applicator to the handle of the product.
A major cosmetics company required rapid production to meet demand. Rogers Foam was ready for the challenge. Our engineering group designed two production machines to facilitate production. The new machine had a ten-second cycle time. A transfer station moved parts between the two tables.
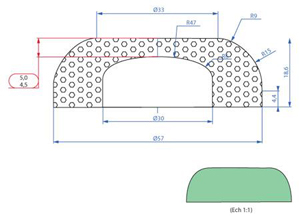
Rogers Foam used the following steps to complete the manufacturing process:
Result
Rogers was given the go-ahead on the final project design in February. The customer placed a stocking order due in September for 1.5 million pieces. Our engineering department built two machines in three months. This allowed us to produce 100,000 parts per week to precise specifications using three shifts from June to early September.
If you would like to download this case study as a PDF, please click here.